How to choose the right industrial mixer for your application?
Not all applications are made equal, but almost all chemical applications can see an improvement in chemical efficiency, by incorporating an industrial mixer, somewhere in the process.
By their very nature, industrial mixers create agitation or blending into a containment vessel which adds a number of benefits. This could be speeding up the pH neutralisation process, to reduce the required contact time; improving the contact time of powder blending or simply keeping a lime solution in suspension, maintaining an isotropic solution or acting as a polymer makeup mixer.
With so many different applications for industrial mixers, how do you select the right mixer for the correct application type.
What are the different types of Industrial Mixer?
Industrial mixers come in many different types. We supply and manufacture the following types of mixer:-
- Stumping mixers
- Hand mixers
- Air Mixers
- Electric high speed industrial mixers
- Electric geared industrial mixers
Hand Operated Mixers (Stumping & Rotational)

A hand operated mixer mounted on top a DT100 dosing tank.
Hand mixers are pretty much as described, ie. hand operated rotational mixers which are used when small volumes are needed to be mixed. They are suitable for a wide variety of tasks and totally unsuitable for many more. The speed of rotation is entirely dependant on how quickly the operator can turn a handle and normally surface area and shear factor aren't considered as problematic. Where highly viscous liquids are being turned, it can be difficult for an operator to gather enough initial torque and really, hand operated mixers should be limited to the most basic of tasks.
Stumping mixers are an alternative to a hand mixer, in that they provide the ability to operate vertically. A stumping mixer is good for dousing and obviously offer little in the way of torque shear as there is little or no rotational energy. Stumping mixers are normally reserved for applications such as small quantity reagent make-up or powder blending applications, due to the limitations stumping mixers have in operational use.
Air Operated Mixers
High speed mixing applications can be achieved by using an air operated mixer. These are devices that use a compressed air source to turn a shaft which agitates the solution. It is different to where air is introduced directly into the vessel to cause agitation such as blowers or aeration units.

An air operated mixer where the compressed air source is used to drive the mixer shaft and propellor.
Air operated mixers are designed to operate where process mixing has to take place in a location where it's not viable to use an electrically operated mixer, and mainly for the industrial agitation of liquids in hazardous areas.
One of the key benefits of an air operated mixer is that the rotational speed of the shaft can be controlled by increasing or restricting the air flow to the mixer which is a manually adjustable operation. On the negative side the use of compressed air to provide rotational energy is both inefficient and not suitable for slow speed agitation of highly viscous solutions.
When specifying an Air Mixer for duties, full consideration must be given to the application including both the process chemistry and the environment where the application takes place. As such if you're considering an air mixer for your application please get in touch with our friendly sales team who will be able to assist.
High Speed Industrial Mixers
High speed industrial mixers are excellent devices for mixing liquids together as well as mixing powders into liquids. Installing a high speed industrial mixer into a process can result in improved reaction times for pH neutralisation applications; more efficient use of chemicals in processes and improved results from existing processes.
A high speed industrial mixer uses a marine style propeller which forces the liquid down into the tank. The elements in the tank are forced together in a vortex which creates a very efficient mixing effect.
To provide efficient mixing, the propellor has a very high rotational speed. This makes a high speed mixer excellent for mixing liquids together or for mixing liquids and powders together. As the propellor has a very high rotational speed, it also has a very high sheer factor. This makes a high speed mixer totally unsuitable for mixing polymers or viscous solutions. For polymer mixing or applications requiring constant agitation, such as keeping lime solutions in suspension, we recommend using a geared industrial mixer.
In addition to the high speed mixers having a high shear factor, the propellor also uses a liquid ballast mechanism when operating, meaning that the high speed mixers should not be operated in a tank where no liquid is present. If the process that's being mixed has the possibility of operating where no liquid is present, we strongly recommend that a level controller and level electrodes are installed into the process tank to prevent the mixer from running when the liquid level is below the ballast point of the shaft and propeller.
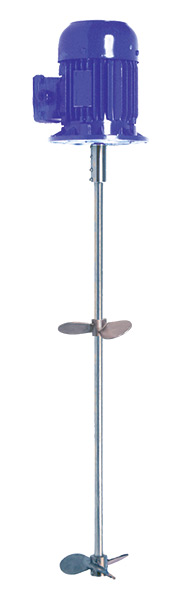
A direct drive high speed mixer fitted with 2 x high speed impellers. This model of mixer was specfied for a neutralisation application a cylindrical vessel.
When deciding on the size of the high speed mixer to suit the process, there are a number of factors that are critical. These include:-
- Liquid Viscosity (cP)
- Specific Gravity (SG)
- Tank Type (cylindrical or rectangular)
- Tank Dimensions
- Tank Volume (m3)
- Mixer Orientation
- Tank Baffling
With these factors considered alongside the industrial mixers power and speed combined with the propellors diameter and pitch we help you calculate the correct mixer type for the application. For instance the amount of power propelling the mixer is dependant upon the volume of fluid that is required to be mixed, and the environment that it is mixed in, eg. a baffled or rectangular tank will provide a better mixing environment than a straight sided cylindrical tank. Offsetting the high speed mixer from the centre in a cylindrical tank is better than a centrally located mixer in the same tank.
Each industrial mixer we manufacture is made to order, in our factory in the UK, so we can incorporate any adjustments required, regarding fitting secondary propellors for larger volumes, specifying forced induction motors for use with inverters or even using food grade lubricants.
As one common application is supplying industrial mixers for pH neutralisation, where concentrated chemicals are used, in these instances we supply the high speed mixers with a chemically resistant coating on both the shaft and impeller.
Slow Speed or Geared Industrial Mixers
Slow speed or geared industrial mixers worked differently to the high speed industrial mixers. Rather than utilising a high speed marine style propellor to force the liquid to the bottom of the tank to provide the in tank agitation, a geared industrial mixer or slow speed industrial mixer, provides a high torque, a slower rotational speed and a large surface area to provide a paddle mixing effect.
Slow speed or geared industrial mixers are desirable mixers for keeping solutions in suspension; mixing viscous solutions and for polymer make up tanks. All applications which benefit from a low rotational shear, high torque or continual operation.
Geared industrial mixers can also be used for pH neutralisation and other process applications, as they provide a gentle and continual mixing of liquids. As they utilise a reduction ratio gear box, some of the geared mixers are suitable for continual operation when the liquid ballast or baffle isn't in place, making installation and operation simple.

A slow speed or geared mixer fitted with 2 x 16" diameter stainless steel impellers and a 140 RPM output for use in a pH neutralisation application.
When considering a geared mixer for industrial duties, a similar list of considerations are used as with the high speed mixers:-
- Liquid Viscosity (cP)
- Specific Gravity (SG)
- Tank Type (cylindrical or rectangular)
- Tank Dimensions
- Tank Volume (m3)
- Mixer Orientation
- Tank Baffling
- Liquid Properties
As the geared industrial mixers use a flat bladed impeller, the specific gravity, liquid viscosity, and liquid properties (specifically if the liquid is isotropic) combined with the tank volume, are key considerations when sizing the mixer. By calculating the surface area of the flat bladed impeller against the volume of liquid and the liquid properties, we can calculate the torque required and the size of the geared mixer.
Some applications require a dual impellers which has an impact on the motor sizing (the surface area has an RMS relationship with the required torque) as well as the rotational speed.
It's also worth noting that each geared mixer is designed and engineered at our facility in Stafford UK, so we can ensure that any specifics in your application can be accommodated for. Additionally, our geared mixers with flat bladed impellers are not tapered, which means that they provide excellent agitation from a narrower rotational diameter and a reduced shear factor.
The liquid properties is a very important consideration. Some liquids are isotropic and require a higher initial torque but benefit from a higher rotational speed, where others require a slower rotational speed, such as a flocculant mixer or slow speed geared mixers, to make up poly aluminium chloride or PAC.
Calculating the shear factor for a flocculant mixer or a PAC make up mixer is important. If the shear factor is too high, it can result in trimming of the poly aluminium chloride, which reduces its effective surface area and thus operational efficiency. We recommend a slower RPM rate for flocculant mixers with impeller sizing to suit the tank volume.
As each geared mixer is designed and engineered at our premises in Stafford, in the UK, we are able to modify the specification of the geared mixer to suit your application. Commonly, this includes supplying mixers with a plastic coating, making them suitable for use in concentrated chemical reagents, changing the gear ratio to suit the application required, modifying the impeller diameter to suit conical tanks or other requirements, such as increasing the number of impellers to suit the application, as well as fitting the geared mixer with food grade lubricants, for use in food and beverage applications.
Geared mixers are highly versatile. They can be used as stirrers for keeping lime solution in suspension; to increase process efficiency in pH neutralisation applications, as well as flocculant mixers for PAC make up vessels. For more information on sizing mixers, please don't hesitate to get in touch with our sales team.
How to install a high speed mixer
A guide to the mechanical installation of high speed mixers into tanks and process vessels.
How to install a geared mixer
A guide to the mechanical installation of flange mounted geared mixers into tanks and process vessels.