Small Effluent Treatment Systems and pH Neutralisation Skids
As providers of instrumentation and control equipment designed specifically for use in water treatment, effluent treatment and process control, our equipment is often used in the process plant for industry.
Large Effluent Treatment Systems
Providing bespoke effluent treatment systems and processing plant is something that many of our customers excel at and is an area beyond the scope of our supply.
If you have a requirement for a large effluent treatment system - then please don't hesitate to let us know and we'd be happy to recommend a shortlist of trusted companies.
Effluent Treatment and pH Neutralisation Design
We are able to supply small effluent treatment systems or pH neutralisation skids, designed and manufactured specifically for your process.
Each system begins in consultation to understand the process requirements. A P&ID drawing is produced and agreed as well as the technical drawings showing sizes, dimensions, sensor mounting points and any inlets and outlets to ensure that the equipment provided can be integrated into your process.
When the control requirements are established, the drawings for the control panel layouts, PLC user interface designs and electrical switch grader are submitted. There is more information on the Control Panel design and build here.
When agreement is reached on the drawings, we begin the manufacturing and assembly process.
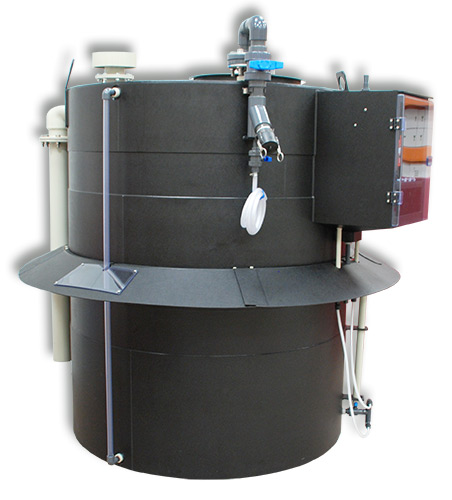
Small Effluent Treatment Systems
Typically small effluent treatment systems use a pH neutralisation tank which is manufactured to your specification. This includes any specified inlets and outlets with included fitting types, such as flanges, unions or threaded connections.
Each tank can be supplied custom fabricated to ensure the desired capacity and treatment times can be reached or to account for the physical space available.
We can supply the pH correction tanks complete with tank mounted pH sensor, other types of tank mounted sensor, level control electrodes, and high speed mixers or geared mixers. If you require a specific piece of equipment to be installed on the tank such as blowers, aerators or other items then we can mount free issued equipment directly to the tank at our Stafford factory.
In addition to control equipment, the tanks can be manufactured with any necessary safety considerations, including double confinement, bunds, rain skirts, baffles or internal shelving.
For safe handling and safe installation we can manufacture our tanks complete with floor mounts to secure into place, lifting points for safe transfer via a crane and on reinforced platforms, fabricated to forklift standards.
The electrochemical sensors and process control equipment will typically feedback to a control panel which can be mounted inside a kiosk secured to the tank itself, or the control panel can be located externally to the tank.
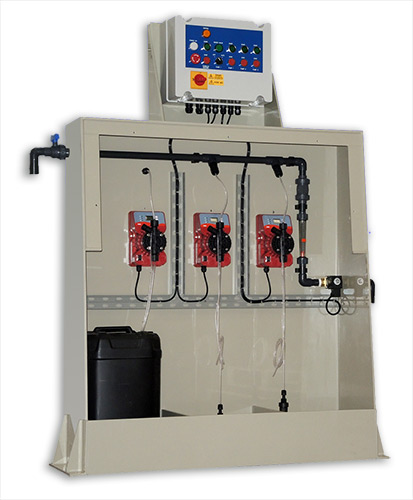
pH Correction Skids
pH correction skids or pH neutralisation skids are typically fabricated enclosures which include a bunded area for storing chemical reagent vessels. The number of bund chambers and the size of the chemical vessels that can be stored varies depending upon the application.
The dosing skids can incorporate a flow through within the skid itself allowing either the sensors to be mounted inline, or for the chemical injection potions to be mounted inline. The flow through normally includes process connections and isolation or actuated valves to control the flow through the pipeline.
The process control is taken from a control panel which is either integrated into the dosing skid or which can be mounted away from the skid itself.
The control equipment including the dosing pumps, solenoid valves or actuated valves can be located through a transparent screen which can be manually removed, or only accessible via a key lock entry. In addition the control panels can be secured by key-switch or from password protection depending upon the nature of the system.
As an alternative to a flow through system, we can provide dosing line to cover the distance to process vessels.
System Testing
All the systems manufactured are subject to electrical testing, usability testing and wet testing, prior to despatch. We welcome scheduled visits during every stage of the design, build and testing of the systems, to ensure that they are being developed to your satisfaction.
The electrical testing will ensure that the systems are working both from a process perspective and from a safety perspective. The usability testing ensures that if the system needs operator involvement, the requirements are simple and clear both from a control panel design and HMI perspective. The wet testing ensures that the system is both leak and pressure tested.
System Delivery
We work hard to deliver precision measurement and control equipment designed and manufactured to integrate with your process. When the equipment has been signed off from testing, we ensure that the plant can either be collected or delivered to your premises in the same condition it left our factory.
We work closely with our logistics provider to make our systems single location deliveries. This means that once the system is loaded to the transport, the only time it is unloaded is at your premises - this is designed to eliminate the possibility of equipment being damaged in transit, improper stacking or handling.
On-Site Commissioning and On-Site Servicing
When the system has been unloaded and installed, we can provide an on-site commissioning service to ensure that the supplied equipment can be operational, without unnecessary delay and certified for process applications.
With on-site commissioning, a senior service engineer will be involved during the design phase, working with manufacturing and will conduct the final equipment testing prior to despatch. This means that when the senior engineer comes to your site to commission the equipment, they have full visibility on the requirements, design and manufacture of the system, so that integration is seamless and commissioning can be completed with a full understanding of the project requirements.
To ensure that the equipment remains operational - we can provide on-site servicing and calibration visits on a schedule, suitable for your requirements. This will ensure that the equipment can expect a long operation life of accurate automated process control and with certification, traceable to national standards.