How to install a High Speed Industrial Mixer
Our TM4-2 High Speed Industrial mixer in a custom polypropylene tank; this version is fitted with 2 x 8" marine style propellors.
Mechanical Installation
First check that the T.M. mixer coupling allen screws securing the motor and shaft are tight. Also that the allen screws in the propeller are tight.
It is essential that when installing the mixer on the tank, it is not lifted by the shaft, as the weight of the motor may cause the shaft to bend.
The motor or gearbox should fit firmly on the bridge or tank support and be properly located so there is no tendency to rock or move about.
High speed mixers ( 750, 960, and 1450 R.P.M. ) should never be run dry or in the air. Always ensure the mixing tank is completely full, it is recommended that at least 3/4 of the shaft be always immersed in the liquid.
It is not recommended that high speed mixers be installed in pumping tanks or sumps with varying levels.
If installed in vessels of varying levels, a low level cut-out protection must be installed. On start up, the propeller must rotate clockwise when viewed 'down the shaft’ so pushing the liquid down the vessel.
Electrical Installation
Before connection to an electrical supply, check that the mains supply type, voltage, and frequency match that shown on the motor name plate.
All mixer electrical supplies, either single or three phase, should be via suitable motor starter, with overload protection to suit the motor in use and hence prevent the possibility of permanent motor damage. Local safety stop buttons and isolation should be fitted so the mixer can be easily stopped, in case of emergency.
All local electrical regulations must be adhered to. Installation should only be carried out by a qualified electrician.
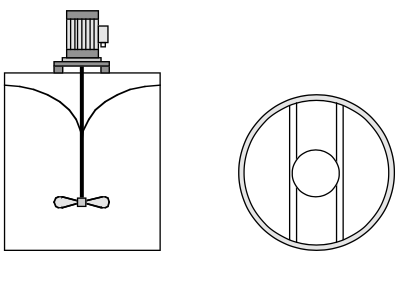
Mixing Powders
Installed with the shaft mounted vertically on the centre line of a vessel without baffles.
With rotation clockwise when looking down the shaft so fluid is pushed down the vessel.
This installation creates a circular vortex suitable for wetting light powders which normally tend to float but are drawn into the vortex. This position is not recommended for other types of mixing.
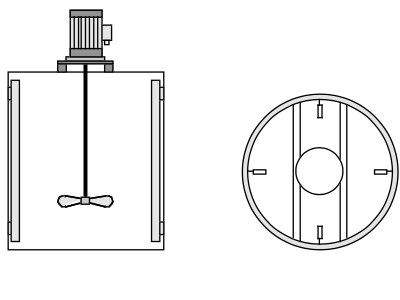
General Mixing Applications (Baffled Tank)
Installed with the shaft mounted vertically on the centre line of the vessel.
Fitted with four strip baffles mounted vertically 90° apart with rotation clockwise when looking down the shaft so fluid is pushed down the vessel.
Baffles should be approximately 1/12 the diameter of the vessel and spaced out 1” from the wall.
This installation creates a turbulent fluid regime ideal for most mixing applications.
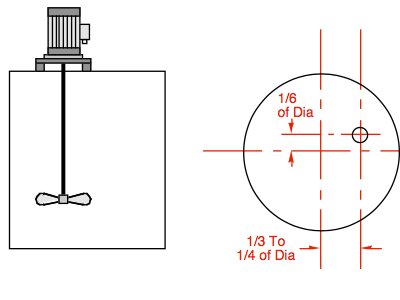
Without A Baffled Tank
Installed with the shaft mounted vertically off centre without baffles with rotation clockwise when looking down the shaft so fluid is pushed down the vessel.
The exact position depends upon the particular application and tank size.
Provides good mixing without baffles. This technique places the propeller in a position which provides an acceptable flow pattern but inferior to a fully baffled tank.
Good for general purpose mixing applications
High Speed Industrial Mixer Range
You can view our range of high speed industrial mixers here.
Our mixers are all manufactured at our facility in Stafford, UK. We frequently manufacture customised mixers for customers, including air mixers, mixers with dual or triple propellors for mixing very large volumes, and mixers for concentrated reagents. If you need a mixer for a specific application that is not covered in our industrial mixer range, then please click below to submit some more information, or please don't hesitate to call or email.